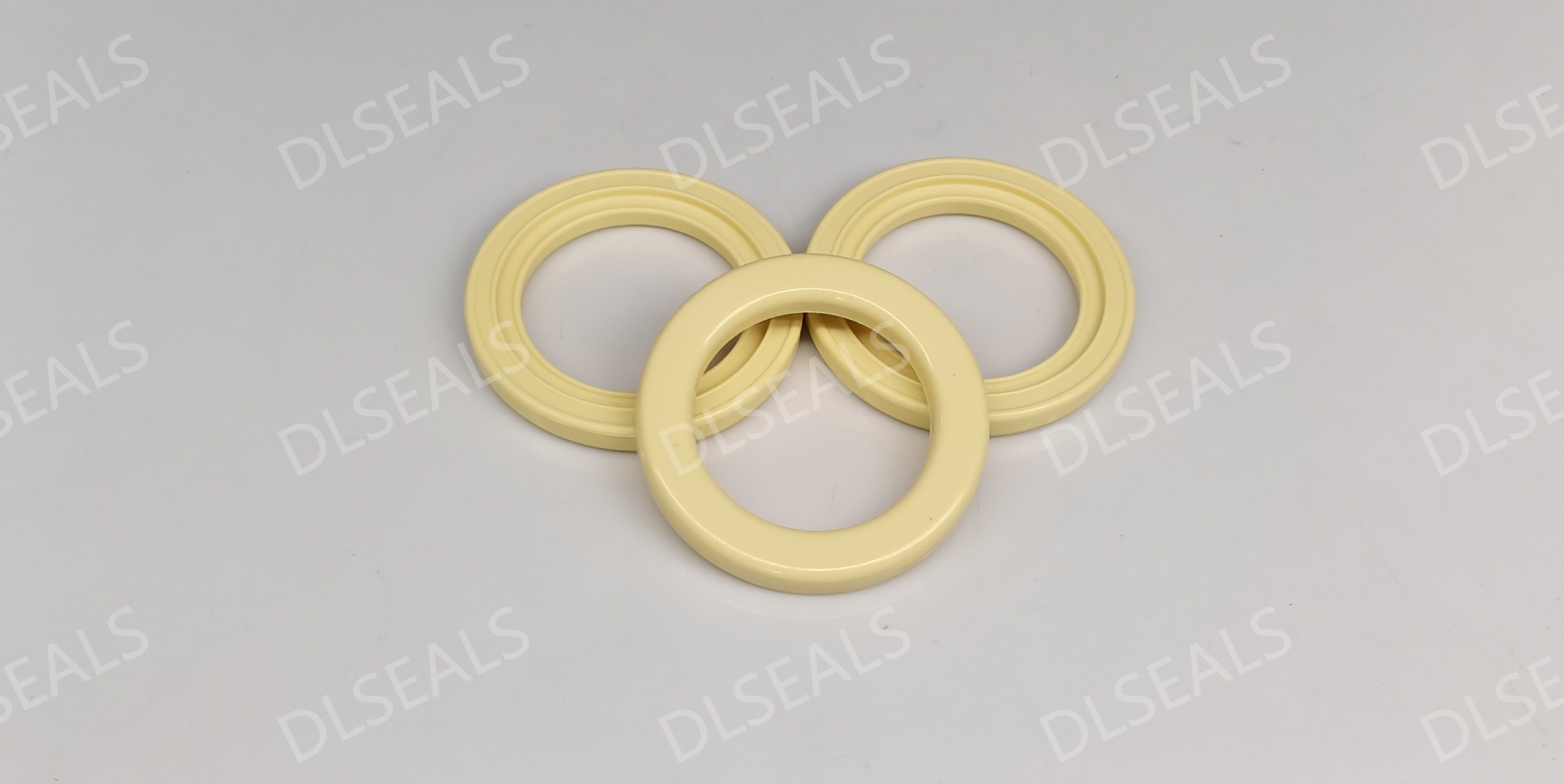
引言
密封圈作为一种关键的密封元件,被广泛应用于各类机械设备、汽车工业和航空航天领域。其加工工艺直接影响到密封圈的性能、耐用性和经济性。本文将深入探讨密封圈的加工工艺,包括常见的加工方法、工艺步骤、材料选择及其对最终产品质量的影响。
1. 密封圈加工工艺概述
密封圈的加工工艺主要包括以下几个步骤:
-
材料准备:
- 原材料:密封圈的材料通常为各种橡胶或塑料,如丁腈橡胶(NBR)、氟橡胶(FKM)、硅橡胶(SI)等。
- 材料处理:原材料可能需要经过预处理,例如混合、加热或冷却,以提高加工性能和材料特性。
-
模具设计与制造:
- 模具设计:根据密封圈的设计图纸制作模具。模具设计需考虑到密封圈的尺寸精度、形状复杂性及材料的流动性。
- 模具制造:常用材料有钢、铝等,通过CNC加工、EDM(电火花加工)等技术制成模具。
-
成型工艺:
- 压缩成型:将橡胶材料放入模具中,通过加热和施加压力使其固化成型。适用于大批量生产和标准密封圈。
- 注射成型:将加热熔融的橡胶注入模具中,通过压力和温度使其固化。适用于复杂形状和精密度要求较高的密封圈。
- 挤出成型:橡胶材料通过挤出机被挤出成型,然后经过切割和硫化处理。适用于长条状密封圈和大尺寸密封件。
-
后处理工艺:
- 硫化:通过加热硫化剂使橡胶材料发生交联反应,提高密封圈的耐温性、弹性和强度。
- 修整:去除成型过程中产生的多余材料,如飞边、毛刺等,以确保密封圈的精确尺寸和光滑表面。
- 检查与测试:对成品密封圈进行质量检查,包括尺寸检测、物理性能测试(如硬度、拉伸强度)以及功能测试(如泄漏测试)。
-
表面处理:
- 涂层:根据需求,密封圈的表面可以涂覆防护层,以提高耐磨性或耐化学性。
- 清洗:清除密封圈表面的杂质和污垢,以确保密封效果。
2. 关键加工技术及其影响
-
模具制造技术:
- CNC加工:高精度的计算机数控加工技术可以确保模具的精确度和重复性,提高密封圈的尺寸稳定性。
- EDM技术:电火花加工技术用于加工复杂的模具形状,尤其适用于硬度较高的模具材料。
-
成型技术:
- 压缩成型:适用于大规模生产,操作简单,但对于复杂形状和高精度要求的密封圈可能存在一些限制。
- 注射成型:能生产高精度和复杂形状的密封圈,生产效率高,但对模具要求较高,且设备投资大。
- 挤出成型:适合大批量生产标准化产品,成本较低,但对产品的尺寸和形状有一定限制。
-
硫化工艺:
- 热硫化:通过高温硫化剂交联,提高材料的物理性能和耐久性,但需要长时间的加热。
- 加压硫化:在加热的同时施加压力,可以缩短硫化时间,提高生产效率。
-
后处理技术:
- 修整:包括去飞边、磨光等操作,影响密封圈的外观和功能。
- 测试:包括物理性能测试(如硬度、拉伸强度)和功能测试(如气密性测试),确保密封圈符合设计要求。
3. 材料选择与工艺匹配
选择合适的材料对于加工工艺至关重要:
- 丁腈橡胶(NBR):适用于油类介质的密封件,因其良好的耐油性和耐磨性。
- 氟橡胶(FKM):用于高温和腐蚀性环境,具有优异的耐化学性。
- 硅橡胶(SI):适合低温和食品接触应用,具有优异的耐低温性能和生物相容性。
材料的选择将影响到模具设计、成型工艺及后处理步骤的实施。选材和工艺的匹配是保证密封圈性能的关键。
4. 挑战与优化建议
-
模具磨损:模具在长期使用中会出现磨损,影响密封圈的质量。定期检查和维护模具,或使用更耐磨的材料可有效应对这一问题。
-
生产效率:选择适合的成型工艺可以提高生产效率。对于大批量生产,可以考虑注射成型或挤出成型技术,而对于高精度要求的产品,则应使用精密模具和先进的成型技术。
-
材料一致性:确保材料的一致性和稳定性是提高密封圈质量的关键。选择高质量的原材料供应商,并进行严格的质量控制,以减少材料变异对产品性能的影响。
-
环保与成本:在加工过程中,应考虑环保和成本问题。选择符合环保要求的材料和工艺,同时控制生产成本,以实现经济和环保的平衡。
结论
密封圈的加工工艺对于其最终性能和质量具有重要影响。从材料选择、模具设计、成型工艺到后处理步骤,每一个环节都需精心控制和优化。通过深入了解和掌握密封圈的加工工艺,可以提高产品的可靠性和性能,满足不同应用场景的需求,并在市场竞争中获得优势。
【德龙密封温馨提示】密封问题找德龙!密封件厂家,接受定制密封件,从设计到研发,从生产到测试,全系列服务。有更多想了解的信息可以直接联系德龙密封,德龙产品专家竭诚为您服务!
电话/微信:13381546720